Prototyping & Fitting
10 January 2022
5 min read
Share
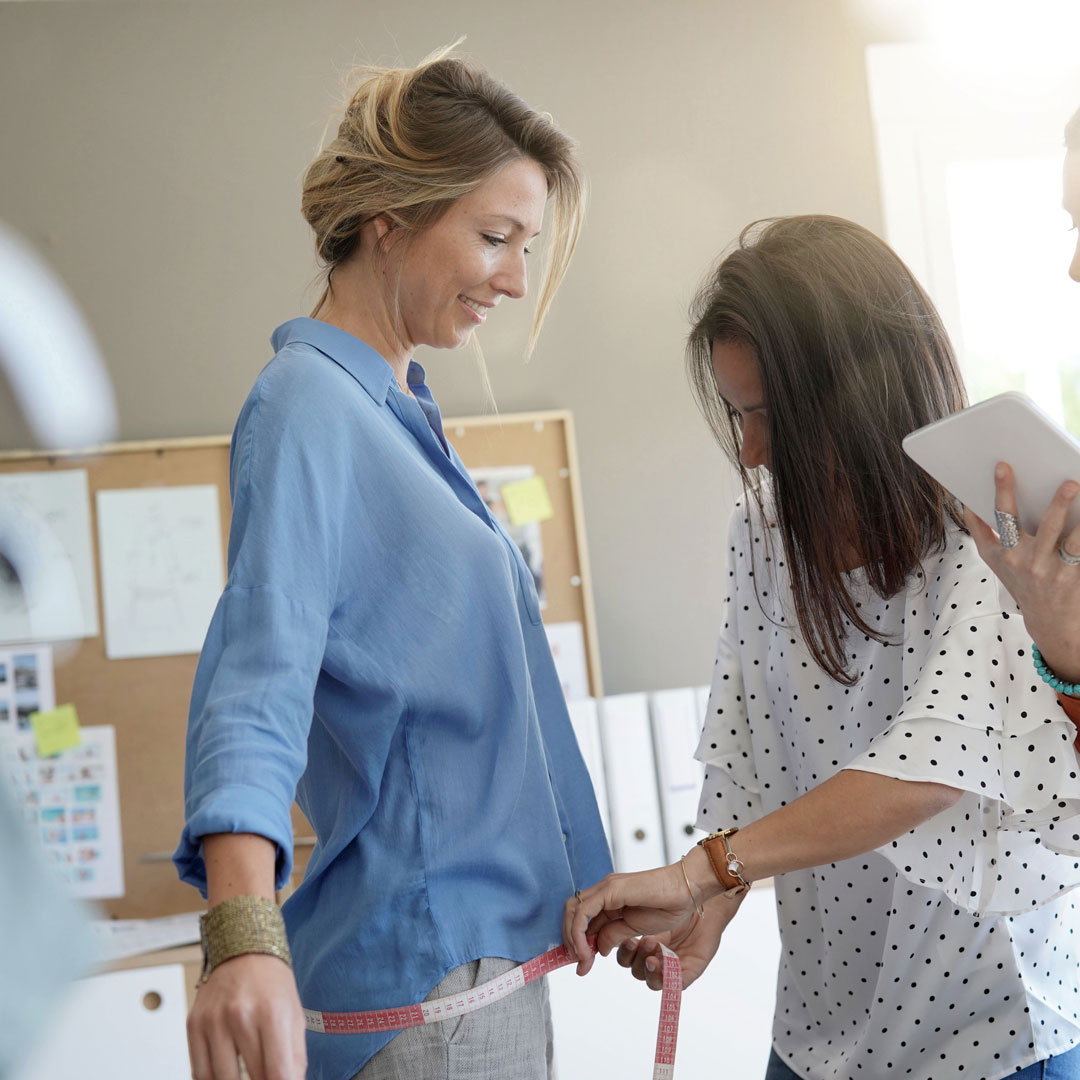
Once the Pattern is done, it is sent to the prototyping team.
Here, the cutter, seamstress, and quality controller officer work together to finally give to life the garment.
The first prototype that is normally realized is called Toile because it is realized on a muslin fabric for test purposes. The use of muslin, a 100% cotton quite stiff fabric, is indicated in case of very difficult pattern construction that supposedly will need a lot of modification. In that case, using an economic fabric for the first tests is very appropriate. Otherwise, it is just a waste of time and the most suggested way to proceed is to use a fabric very similar to the final one selected, in order to properly test the fit, drape, and volumes.
As soon as the Toile is ready, it can be fitted both on a model or a dress form, and all the alterations are normally marked directly on the Toile. Afterward, the pattern will also be changed accordingly and a new proto will be realized with all new modifications.
The last proto is normally realized in the production fabric, with all the correct trims. Once this is completed, the proto is submitted to the final evaluation. On this occasion, the whole team gathers together to discuss the prototype and suggest modifications, but the only figures who effectively have decision-making power are the creative director, the designer, and the pattern maker. Seamstresses normally are present too, for their precious and always appreciated technical support.
Heads up: the whole team gathers only when the final proto is accomplished. The toile is normally just reviewed by the patternmaker itself since it’s a tool of study and a way to check the pattern accuracy.
What are the Main Must-have Machines?
In case you like to sew and you want to realize your own prototypes in-house there are some basic machines and tools that every design studio, even the little ones, should have.
Before rushing to a Sewing shop, I suggest you check out the list below in which we have inserted the main machines that are the most common and used in the fashion industry.
-
- Single Needle: this is the basic MUST-HAVE machine that allows you to sew a garment from beginning to end. If you want to just buy one machine, this will be your obliged choice. Of course, by using one only machine, some finishings will not be as if you use a more adapted machine for that exact operation, but it will allow you to take your garment to life, in a way or another. Single Needle machines normally have the possibility to change the stitching type, in terms of stitch design, tension, and frequency.
- Single Needle: this is the basic MUST-HAVE machine that allows you to sew a garment from beginning to end. If you want to just buy one machine, this will be your obliged choice. Of course, by using one only machine, some finishings will not be as if you use a more adapted machine for that exact operation, but it will allow you to take your garment to life, in a way or another. Single Needle machines normally have the possibility to change the stitching type, in terms of stitch design, tension, and frequency.
-
- Overlocker or Serger: this is a super helpful machine, widely used both with knit and woven fabrics. There are different types of Over Lockers, and they can present 2 to 5 threads. In the case of garments realized in knit fabrics, it is used as the main sewing machine, because with it you can directly sew the fabric pieces together. Whilst, if used with woven fabrics, it is with the aim of stopping the edges of single pieces of fabric from fraying.
- Overlocker or Serger: this is a super helpful machine, widely used both with knit and woven fabrics. There are different types of Over Lockers, and they can present 2 to 5 threads. In the case of garments realized in knit fabrics, it is used as the main sewing machine, because with it you can directly sew the fabric pieces together. Whilst, if used with woven fabrics, it is with the aim of stopping the edges of single pieces of fabric from fraying.
-
- Cover Stitching: this machine is normally used for the hem realization of stretchy knit fabrics. It can present two needles for a double stitched look or three needles for a triple-needle finish. This machine guarantees stretchability and allows covering the raw edges (as the serger does) all in one pass.
-
- Iron with Table: The iron and its table are fundamental tools to assure a good outcome when realizing your prototype. Theoretically, after every new operation, the obtained seam should be ironed, according to specific rules, based on the type of fabric, seam type, and garment piece. It will result extremely useful also for applying the fusible to the fabric, in the absence of a heat press.
-
- Steamer: while iron is mostly used during the construction of the garment, the steamer is a great ally for making sure to eliminate all wrinkles from a finished garment. While the iron requires contact with the fabric and ensures the effect via the heat conduction across the iron plate, the steamer never touches the garment and obtains the same effect by vaporizing it.
Lastly, you might want to start buying second-hand home sewing machines and avoid the industrial ones, which are extremely cumbersome, heavy, and really not the best choice if you are just a starter. And, I forgot to mention, they are also pretty expensive!
In Urth Design Studios we have all the above machines and also the majority of the specialized ones, in order to realize our internal and the clients’ prototypes as complete as possible with all final seams and finishing.
You do not have a trusted Seamstress and you would like to rely on +10 years of experienced sewers? We have different solutions, check all of our services, or Contact Us Today!
Specialized Machines To Outsource
Sewing machines, especially the industrial/professional ones, can be very expensive. This is why, in case you do not want to open your own factory, it will probably be more cost-efficient to just outsource the specialized service you need and avoid buying them.
Among the many sewing machines we can list:
- Button Holing and Button Attaching Machines
- Snap/Rivet Press Machines
- Heat Press Machines
- Laser Cutting Machines
- Bonding Machines
- Bar Tacking Machine
- Thread Embroidery and Needle Punch Machines
- Jet Pocket Machines
- Machines for certain types of special fabrics such as Leather, Denim, etc.
- All sort of printing Machines
- Automated Machines
- Etc.